Volatile Organic Compounds (VOCs) are exceptionally harmful, carcinogenic, and mutagenic substances, widely used in the industry. In concern for the natural environment and human health, lawmakers in most countries have been tightening the norms for handling VOCs and the emissions of VOCs remaining after production processes for many years.
The pursuit of energy efficiency in technologies used to eliminate VOCs is also becoming increasingly important.
Already in the 1970s, catalytic technologies, known as RCO (Regenerative Catalytic Oxidation), began to be used for the elimination of VOCs. After some time, this technology seemed to have reached the end of its capabilities to achieve ever lower emission standards, and – despite advantages over other technologies – began to lose its market share.
The development in recent years of the computing power of microprocessors, sensors, and informatics, combined with the gas flow switching systems developed by Oxydea, has allowed Oxydea’s catalytic technology to become a market leader in eliminating VOCs from production processes.
The following contains an extensive explanation of the topics signalled here.
Important legal information from 2024
On 07.02.2024, the European Commission decided to initiate proceedings for the infringement of a Member State’s obligations by Poland.
“Polish legislation does not correctly transpose several provisions of the directive, including some key principles regarding the conditions of integrated permits and (…), regulations concerning permissible emission sizes, as well as environmental quality standards.”
The failure to fully incorporate the provisions of the IED directive (i.e., the Directive of the European Parliament and of the Council 2010/75/EU of 24 November 2010 on industrial emissions) causes companies to delay investments adapting their installations to new strict emission standards.
Moreover, an amendment to the IED directive, fundamental for the demand for VOC cleaning technologies, is planned for mid-2024. The initiation of proceedings by the European Commission, and the amendment of the IED directive planned for 2024, are very favorable circumstances for Oxydea’s activities.
OXYDEA PRODUCTS
VOC GAS CLEANING INSTALLATIONS
GENERAL DESCRIPTION
We present a solution to the problem of emissions of volatile organic compounds in the industry.
The product is an installation designed to remove, at low temperature (without flame combustion), carcinogenic and mutagenic volatile organic compounds that are produced in a huge number of industrial processes worldwide. The applied technology also allows for the recovery of waste heat generated in the oxidation process. The product works (in simplified terms) by combining:
- catalytic technologies in regenerative reactors RCO/CFRR,
- advanced process control using SCADA software.
Our product is dedicated both to stable production processes and to industrial processes in which significant variability of process gas parameters (flow, composition, VOC concentration) may occur. As a result of the application of follow-up control system and measurement automation, intelligent control algorithms, and precise manufacturing procedures for platinum catalysts with a large active surface area proportional to the volume of the catalytic bed and the cost of the used platinum, Oxydea’s technology can solve the VOC problem.
The RCO/CFRR technology provided by Oxydea can replace the molecular sieve technology currently used for cleaning post-process gas from VOCs. Molecular sieves require, among other things, heavy, problematic to process, difficult to calibrate moving parts. It seems likely to replace molecular sieves with simpler to produce RCO/CFRR reactors, almost devoid of moving parts, cheaper to produce and maintain.
The client receives a ready-to-use technological line for oxidizing volatile organic compounds, launched in their production infrastructure, and integrated with the control of other processes (if necessary). The client pays for the installation that solves the problem with VOC emissions and allows for the utilization of waste heat.
VOLATILE ORGANIC COMPOUNDS
Volatile Organic Compounds (VOCs) are toxic by-products in many industrial processes. VOCs have strong mutagenic and carcinogenic effects. Organic compounds are all chemical compounds containing carbon (in combination with hydrogen), except carbon dioxide, carbonic acid, and a few others. Organic carbon is the carbon contained in an organic compound.
Volatile Organic Compounds (VOCs) are a group of several hundred organic compounds that easily turn into vapor or gas, and their boiling point ranges between 50–250 °C.
The basic unit in which emission levels are expressed is the concentration of pollutants – converted to the mass of organic carbon [mgCorg/Nm3].
NEW EMISSION STANDARDS
According to the Directive of the European Parliament and of the Council 2010/75/EU on industrial emissions (known as IED), and the Environmental Protection Law, setting conditions for integrated permits (i.e., the administrative decision under which companies potentially polluting the environment due to VOC emissions operate) is based on so-called BAT Conclusions (Best Available Techniques). BAT Conclusions are a source of EU law (known as the European Commission’s implementing decision). It includes conclusions on the best available techniques, descriptions of these techniques, information for assessing their applicability, and the permissible emission sizes after their application. In the Official Journal of the EU, BAT Conclusions for several types of activities have been published, these conclusions are binding, introducing stricter VOC emission standards. Companies must comply with the new standards and implement new technologies (BAT) under the threat of high fines.
Oxydea’s technology is mentioned in the BAT Conclusions.
IED 2024 AMENDMENT
Despite only a few years since the last tightening of emission standards, another amendment to the IED directive is planned for 2024. This amendment will be very beneficial for Oxydea.
In the administrative procedure, there will be an obligation for the authority to analyze whether the emission level proposed when applying for an administrative decision (currently usually the most lenient possible within the range defined by BAT) could not be more stringent. In practice, this may lead to discretionary tightening of individual emission standards.
A revision of the BAT reference documents (BREFs, from which legally binding BAT conclusions are created) will be made by 2028 (and then every five years). The assessment must take into account new techniques. The next process of updating administrative decisions and adapting installations will be carried out according to new rules and with new, tightened emission levels.
Public access to information on industrial emissions will facilitate public participation in environmental decision-making, including the choice of technologies for emission reduction. Effective, proportionate, and deterrent penalties for those who violate the regulations are anticipated. Individuals whose health has suffered as a result of intentional or negligent violation of the regulations will be entitled to compensation.
SECTORAL APPLICATIONS
The primary industry for sales will be factories producing colorful plastic packaging using flexographic technologies. This is a large and rapidly growing market, subject to emission controls. Additionally, the cost of electricity for drying surfaces processed by flexography, especially after electricity price increases, constitutes a significant percentage of production costs. Energy cost savings and the recovery of thermal energy are pointed out by potential clients as a significant advantage of Oxydea technology.
Other industries include all sectors utilizing surface coating technologies with paints, etc., such as automotive, steel structures, home appliances, and more.
Moreover, Oxydea technology is applicable in industries such as:
- pharmaceutical manufacturing,
- production of adhesives, sealants, glues, and the application of these substances,
- production of footwear, carpets, linoleum, sound-absorbing coverings, etc.,
- production of varnishes,
- production of printing inks,
- rubber processing,
- extraction of vegetable oil and animal fat,
- impregnation of wood,
- laminating of wood and plastics,
- production of polishes, cleaning agents, deodorants,
- production of pesticides, herbicides
- cement production.
We are ready to collaborate with representatives of the aforementioned industries to tailor the technology to individual needs.
CATALYST
WHAT IS A CATALYST?
A catalyst is a substance that accelerates or facilitates chemical reactions or lowers the energy required for a chemical reaction to occur. In a catalytic reaction, the catalyst is neither consumed nor undergoes physicochemical changes. In the industry, catalysts play a key role in the efficient and economical conduct of chemical processes, allowing for desired outcomes at lower temperatures, concentrations, pressures, etc.
Benefits of using catalysts in the industry:
- Increased Efficiency: Catalysts significantly increase the speed of chemical reactions, translating to higher production efficiency and shorter process times.
- Energy Savings: Catalysts allow many industrial processes to require lower temperatures and pressures, resulting in lower energy consumption and reduced operational costs.
- Reduction of Harmful Emissions: Catalysts help in reducing emissions of harmful substances, such as nitrogen oxides, sulfur oxides, volatile organic compounds, contributing to environmental protection and compliance with environmental standards.
- Product Quality: The use of catalysts enables the production of cleaner and more uniform products, which is crucial in many industries, e.g., pharmaceutical and food industries.
- Innovation and Development: The application of modern catalysts opens the door to creating new materials and products, supporting innovation and technological development.
Without the use of a catalyst, the oxidation of VOCs occurring as waste in industrial processes typically happens at temperatures of 900-1300°C. This is flame oxidation. In situations where the VOC concentration is too low for spontaneous flame oxidation to occur (commonly known as “combustion”), similar to the burning of natural gas in a gas stove, continuous heat must be supplied to the process for VOC oxidation. The heat source is a burner powered by an external energy installation (gas or oil). This is flame-assisted VOC combustion, costly, and requires the use of materials resistant to high temperatures. A separate issue related to thermal combustion is the emission of nitrogen oxides (NOx). Nitrogen oxides, in turn, have an impact on the formation of carcinogenic and mutagenic substances.
Oxydea offers high-quality catalysts made of precious metals: platinum, palladium, and rhodium (Pt, Pd, Rh) for applications in the oxidation processes of volatile organic compounds, arising as waste substances in industrial processes.
RCO/CFRR TECHNOLOGY
DESCRIPTION OF THE TECHNOLOGY
BASIC PRINCIPLE
The product is an installation designed for the low-temperature oxidation of carcinogenic and mutagenic volatile organic compounds, which are produced in a huge number of industrial processes worldwide, and then (optionally) for the recovery of waste heat generated in the oxidation process. The operation of the product is (simplified) based on combining:
- Catalytic technologies in regenerative reactors RCO/CFRR,
- Advanced process control using SCADA software.
RCO/CFRR reactors are nanotechnology and energy-saving algorithms used in large industrial installations.
CATALYST
A catalyst is a substance that allows reducing the energy needed for a chemical reaction to occur, in this case, allowing to lower the temperature at which VOCs are neutralized. More general knowledge about catalysts can be found in this part of our website.
Gas purification occurs in the catalytic reactor RCO/CFRR, in the presence of a catalyst mainly consisting of platinum, at temperatures not exceeding 400°C, and involves the oxidation of VOCs to CO2 and H2O.
The catalyst used in RCO/CFRR reactors is a material nanotechnology, requiring advanced procedures in the manufacturing process. Oxydea possesses unique competencies, making it an independent producer of these catalysts.
SCADA SOFTWARE
SCADA (Supervisory Control And Data Acquisition) is a computer system that supervises the course of a technological process. Its main functions include collecting current data (measurements), visualizing them in a user-friendly interface (UI – User Interface), controlling the process, alerting, and data archiving.
Proprietary algorithms will be applied in a responsive automation and control system based on PLC processors synchronized with SCADA visualization.
The follow-up control system is an automation system whose algorithm implements a certain course of the controlled variable, where this course is not known. The control signal x0 is an unknown function of time. Changes in the control signal x0 do not depend on the process occurring within the automatic control system but are caused by phenomena occurring outside this system. Changes over time in the value of the setpoint w = f(t) are also usually unknown. The values of this function are determined by factors occurring outside the control system. The task of this system is to control the object so that changes in the regulated variable follow the changes in the setpoint. The setpoint is called the leading variable. Such a method of controlling a physicochemical process meets the characteristics of so-called Industry 4.0.
RCO/CFRR
The RCO/CFRR (Regenerative Catalytic Oxidation/Catalytic Flow Reversal Reactor) technology is based on a cyclic process involving:
- Oxidation of gas in the presence of a platinum catalyst (the presence of a catalyst differentiates our technology from the previously used RTO technology), and
- Heat discharge into a ceramic bed
in a symmetrical pair of reactors operating alternately in cyclically changing directions of gas flow.
Once initiated, the process continues autothermically (i.e., “by itself” without the need for external energy input). The gas, purified of VOCs, exits the CFRR reactor at a temperature of about 350°C, allowing for the recovery of waste heat.
PROCESS FLOW
The ceramic bed serves as a heat exchange medium: first by heating the gas to the temperature necessary to initiate the oxidation process of VOCs in the presence of a catalyst, and then by accumulating the heat generated as a result of the VOC oxidation reaction.
In the first cycle, gas containing VOCs flows through the hot ceramic bed of one of the two reactors. The gas is heated to a temperature sufficient for the catalytic exothermic (i.e., with heat release) oxidation reaction of VOCs contained in the heated gas to occur upon reaching the catalyst layer. The hot oxidation products leave the first reactor, flow to the second, and transfer heat to the ceramic bed in the second reactor until the direction of gas flow is reversed through the pair of reactors.
In the second cycle, the direction of the gas flow containing VOCs is changed, now flowing to the second of the pair of reactors. Similarly, as in the first cycle, the gas is heated on the ceramic bed to a temperature sufficient for the catalytic exothermic oxidation reaction of VOCs contained in the heated gas to occur upon reaching the catalyst layer. The hot oxidation products leave the reactor, flow to the first, and transfer heat to the ceramic bed in the first reactor.
Introducing a catalyst into the CFRR reactor means that the oxidation of VOCs occurs at temperatures several hundred degrees Celsius lower (even 500-700°C, depending on the compound) than the oxidation (then flame combustion) temperature without a catalyst.
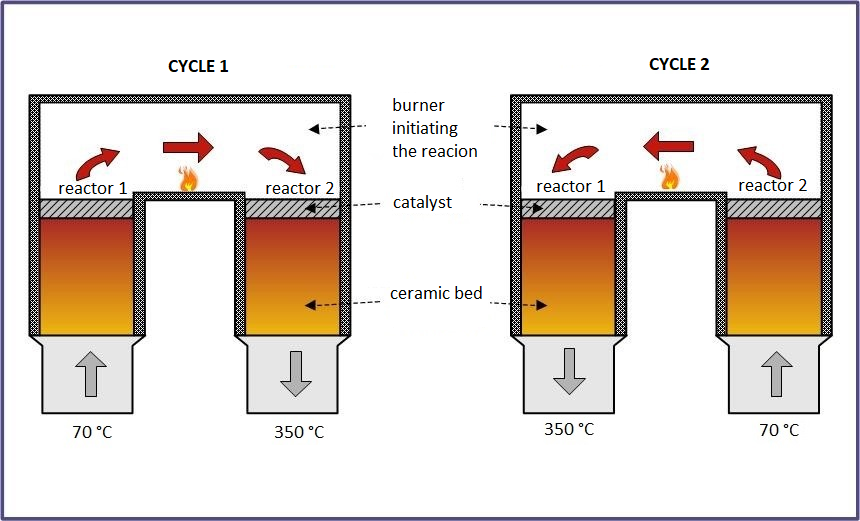
APPLICATION OF CATALYSIS – BENEFITS
- Autothermic process (i.e., without external energy input).
- The possibility of recovering waste heat for production needs, heating buildings, etc., which, in the circumstances of a huge increase in electricity prices and the shortage and price rise of energy resources, allows clients to reduce costs.
- Lowering the temperature of the process, and as a result:
- A significant reduction in CAPEX costs for the solution, eliminating the need for heat-resistant steel, ceramic insulating combustion chambers, etc.
- Substantially extending the solution’s lifespan, thereby reducing OPEX costs, with no overhauls, downtime, or replacement of wearing parts, among other benefits.
- Elimination of emissions of carcinogenic smog-inducing NOX (nitrogen oxides), which is a substantial advantage.
USING THE SCADA SYSTEM – BENEFITS
- Maintenance-free, fully automatic process operation in 24/7/365 mode.
- Effectiveness of autothermic operation across the full (very wide) nominal range.
- Readiness for use approximately 30 minutes after switching on.
- Flexibility to quickly adapt to changes in the production process (new machines, new products).
- User-friendly, understandable graphical user interface (UI).
- Online access for supervision, etc.
- Ease of data analysis.
SCALING
The solution is modular, so in the case of an increase in a client’s production capacity, i.e., an increase in the amount of VOCs, an additional pair of RCO/CFRR reactors is added, and SCADA control is modified.
Modules can be designed for various capacities, for clients with any large VOC emission problem.
The relatively small size and weight of the solution, negligible vibration level, and low risk of fire or explosion allow for installation in convenient or available places in the existing conditions of the client, i.e., without construction work, including above the production space, outside the production hall, etc. The solution will also allow for flexible heat recovery, appropriate to the size, and its redirection into the production process.
TECHNOLOGY COMPARISON
Characteristics of current solutions | Characteristics of the Oxydea solution |
---|---|
Heavy, large-diameter, difficult to calibrate/center rotating (motor-driven) wheel containing sorbent (so-called “rotor concentrator”). | Lightweight solution not requiring motor drive, almost devoid of moving parts, without friction-related issues, without deformation of components due to gravity and large temperature changes. |
Rotating wheel with a large diameter, containing sorbent (so-called “rotor concentrator”) requiring very precise fitting to the process gas channel; the only seal is a layer of teflon. Particularly problematic is matching the thermal expansion of the wheel (rotor concentrator) and the gas channel | Significantly smaller gas channel diameters reduce the effects of potential leaks, which are eliminated by an appropriately selected sequence of channel valve switching. | Significantly smaller gas channel diameters reduce the effects of potential leaks, which are eliminated by an appropriately selected sequence of channel valve switching. |
The process includes desorption, which requires additional energy. Only part of the device (4 or 5 out of 6 sections of the wheel, minus the surface of the supporting structure required to be maintained in motion but not participating in physicochemical processes) is involved in cleaning the process gas from VOCs (adsorption process), the rest undergoes desorption. | The device is fully utilized all the time (100% of the active surface participates in physicochemical processes). |
Sorbent requires replacement because its absorbency decreases over time. It is estimated that replacement is necessary every 6 months. | The catalyst can operate for many years without loss of oxidation efficiency. It is estimated that a properly used installation can operate for 5 years without the need for catalyst replacement. |
Desorbed VOCs are always oxidized by flame, which requires parts of the device where combustion occurs to be made from heat-resistant materials. Flame combustion temperature is 800-1200 Co | Flame heating of the process at low VOC concentrations is done up to 400°C (usually up to 350°C), so in principle, it does not require special materials. In smaller devices (for smaller flows, below 10,000 m3/hour), electric heaters with precise power control can be used. |
The precision of assembly and the weight of the device significantly limit the possibilities of location. The external temperature’s effect on the thermal expansion of the gas channel and the resulting mismatch to the thermal expansion of the wheel containing sorbent (rotor concentrator) must also be considered. | Relatively low weight and lack of external conditions affecting the quality of operation allow for flexible device installations, e.g., above the production hall, outside the production hall. |
Used sorbent is a hazardous waste requiring disposal. | Used catalysts, consisting of platinum and a mineral substrate, are 100% recyclable with ease. |
Future emission standards may limit the use of other technologies. | Future emission standards may promote Oxydea technology, especially after its inclusion in the Innovation Center envisioned in the revised IED (in 2024), which will create trends in environmental protection and emission reduction methods. |
FOR INVESTORS
CO-INVESTORS FOR THE CONSTRUCTION OF A DEMONSTRATOR
We plan to build a demonstrator of the RCO/CFRR technology, through which potential clients can see that the optimal decision for solving the problem of new VOC emission standards would be to entrust the solution of this problem to Oxydea.
Currently, investors in the company include a pre-seed venture capital fund and a business angel. We have declarations of equity participation in the project from a producer of complete technological lines for paint coating and a constructor of precision steel structures (including gear transmissions). We are looking for co-investors to finalise the financing for the construction of the demonstrator. Oxydea has the support of partners with investment experience, and is ready to accept financing on terms commonly used in venture capital investments without unnecessary delay
BUSINESS MODEL
Oxydea plans to act as the general contractor for industrial air purification installations from volatile organic compounds using its own know-how for the most margin-rich parts of the product: catalyst production and CAD and SCADA design. The company plans to outsource the following areas
- construction of steel structures,
- thermal insulation services,
- installation assembly services.
This outsourcing is planned to be entrusted to an experienced and verified business partner who currently operates (for over 15 years) as a manufacturer and general contractor of full installations for the paint industry. It has the appropriate production and personnel facilities. From the beginning, sales will be planned based on the distribution channels of the aforementioned partner, both as the sale of separate installations for solving VOC problems and as combined sales, i.e., integrating installations to solve VOC problems into installations for the paint industry. Such a solution is a significant facilitation for entering the paint coating market. Additionally, outsourcing of precise steel elements will be entrusted to another partner with many years of experience in producing, among others, components for gear transmissions.
CREDIBILITY
Oxydea closely cooperates with partners: Sarmatia Ventures and a business angel from the Cobin Angels network. These partners provide know-how in finance management, strategic planning, cooperation with large industry, collaboration with venture capital, etc.
Oxydea maintains contacts with clients from the flexographic industry, actively operating in the flexographic industry chamber, and with a company (global holding) from the cement industry. These companies are interested in implementing technologies that solve VOC emission problems in accordance with new standards. Cooperation with target customers allows for better tailoring of technology to market needs and to ISO standards and others.
Oxydea maintains contacts with scientific units (Łukasiewicz Research Network, and others), which may prove helpful in solving potential individual problems during the Project implementation, requiring narrow but deep scientific knowledge.
Oxydea was created as a spin-off of NataLab Sp. z o.o., which was established in 2017 to conduct a research project on processing printed circuit boards and metal recovery from them. Within the scope of these studies, research on the RCO/CFRR technology intended for cleaning gas resulting from the processing of printed circuit boards was included. The NataLab project had a budget of about 4 million PLN. In the mentioned research project, a huge potential of the RCO/CFRR technology improved by NataLab was identified for commercial use in many industries. Therefore, it was decided to separate the RCO/CFRR business line into a new company, Oxydea, to facilitate financing acquisition and separate the risk of developing printed circuit board processing technology.
NataLab obtained business angel financing and pre-seed financing and was publicly evaluated, including:
- winning the Start-up Challenge at the European Economic Congress,
- inclusion in the InCredibles mentoring network, sponsored by Sebastian Kulczyk.
Contact us to get a presentation for investors.
Contact
We invite you to our office in Warsaw, in the Varso building, in the global ecosystem of innovative startups Cambridge Innovation Center.
Contact us, both about the services we provide and business proposals regarding the expansion of our activities.
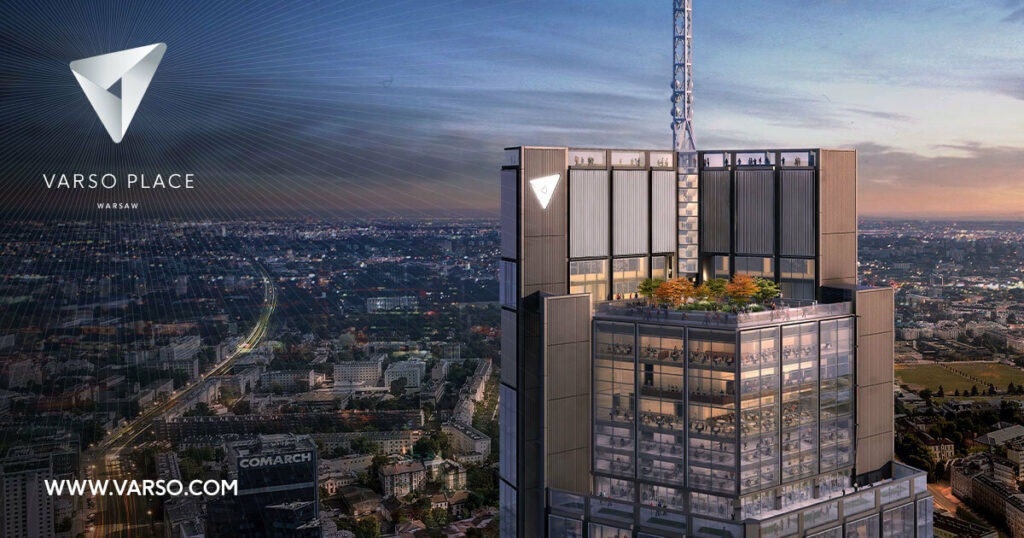
Registration data Oxydea Sp. z o.o. KRS 0001003124 NIP 5213993105